Get the low down on our down
Not all down jackets are created equal. Learn more about the differences and how we work with ethical down.
As a chilling wind blew through the camp, the snow-covered landscape still and silent, Fjällräven founder Åke Nordin wished he had a warmer jacket. He made a promise to himself: to create a jacket that when you are encased in its embrace it’s impossible to feel the cold. The following winter Åke was back in the winter wonderland of northern Sweden, this time armed with the Expedition Down Jacket, packing a mighty 600 CUIN of high quality down. And guess what? He didn’t freeze. In fact, he felt warm and cosy despite the sub-zero temperature nipping away at the tent.
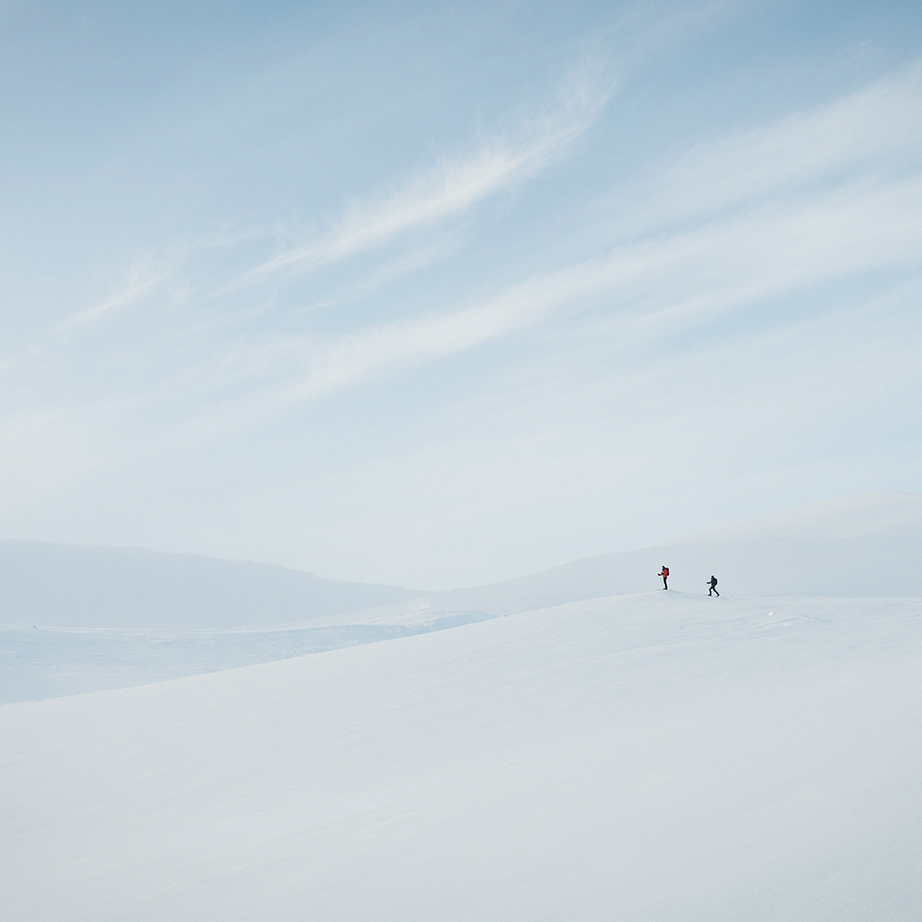
This was 1974 and it marked the start of our down journey. Nowadays we use it in a whole range of products from sleeping bags, trousers and heavy weight winter jackets, like the Expedition Down Jacket, right through to lightweight vests and spring jackets. It’s extremely versatile. We can adjust the amount of down we use depending on whether we’re creating a really warm garment or a layering piece.
How does down work?
Nature knows best. It’s created amazing materials, with down being one of them. Birds have long enjoyed the warming presence of down feathers under their regular longer ‘flight feathers’. These super-fine feathers are basically air trappers and thus they’re incredibly insulating.
When you look at a down feather under a microscope it looks like a tree. The stem, the part that attaches to the bird’s skin, is the trunk. Then a plethora of small fibres branch out into ever-smaller fibrils. This loose structure traps air in the spaces between the fibres and it’s the air that then insulates against heat loss.
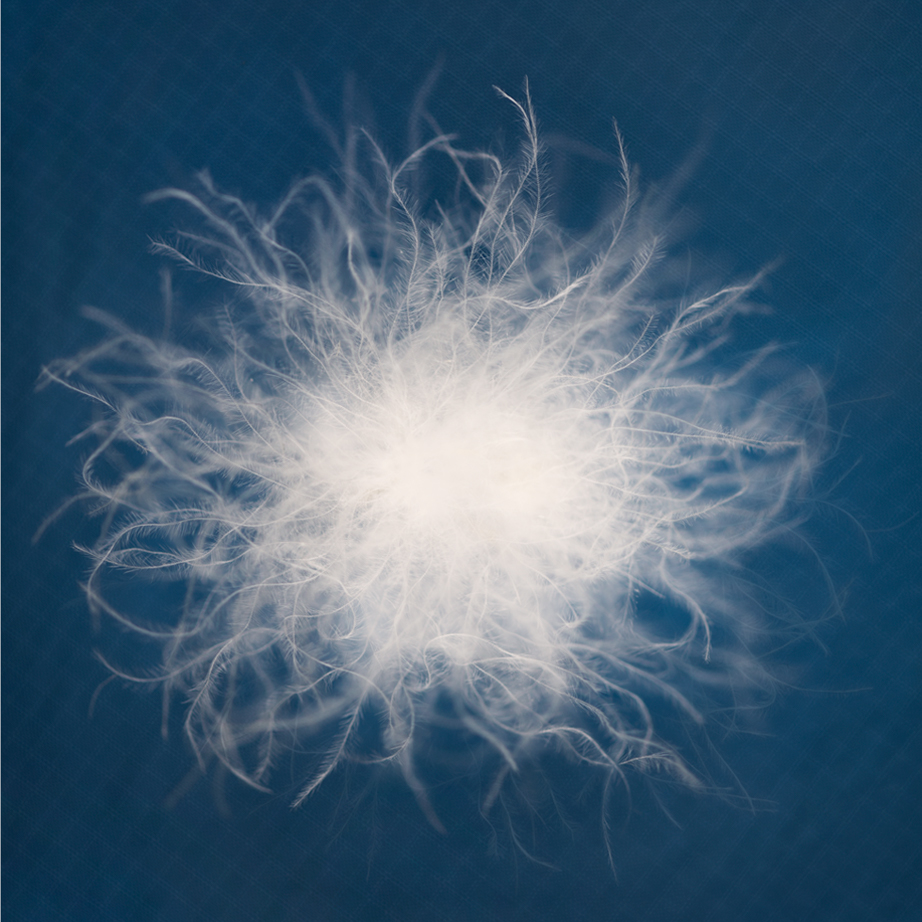
The warmth of a down jacket, i.e. its insulating power, is measured in cubic inches, commonly referred to as CUIN or fill power. Our jackets are between 600 and 800 CUIN. So for a 600 CUIN jacket one ounce of the down inside the jacket takes up 600 cubic inches. The higher the number the more air the down traps. So you may think that the higher the CUIN number, or fill power, the warmer the jacket. And for the exact same jacket, with the same outer material and internal structure, this is true. But when comparing different jackets it’s not as simple as this.

The fabric and structure used to encase the down affect its fill power.
Shufei Wang
Fjällräven Product Developer
“The fabric and structure used to encase the down affect its fill power,” says Shufei Wang, Fjällräven Product Developer. “When we classify our down according to CUIN, we divide it up based on the ratio of down to regular feathers. So in our 600 CUIN jackets, for example, we have 80% down and 20% feathers. In our 800 CUIN jackets we have 95% down and 5% feathers. But a higher CUIN number doesn’t necessarily mean you get a warmer jacket.”
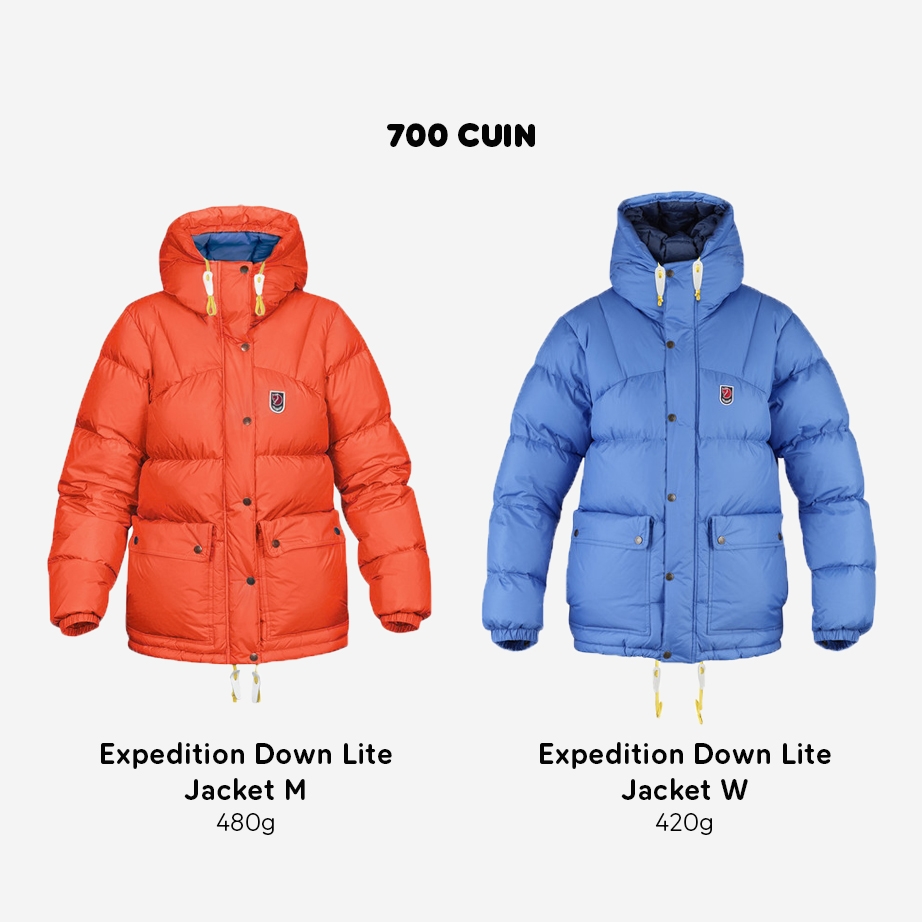
"So if you compare our current and new Expedition Down Jackets for men and women the CUIN number is steady at 700, but the weight of the down varies from 420g to 730g. There are three factors that affect the insulation potential of a jacket,” says Shufei. The fill density – basically how much down is actually stuffed inside the jacket – the product’s construction and the type of fabric that holds the down.

The structure is actually really important and something we're constantly testing to look for improvements. We use three different techniques. The first, the most commonly used, is a sew-through construction. “We create tunnels or columns in the jacket which we then stuff with down. This creates an extremely light garment that’s easy to pack, but there are cold spots on the seams between the columns,” explains Shufei.
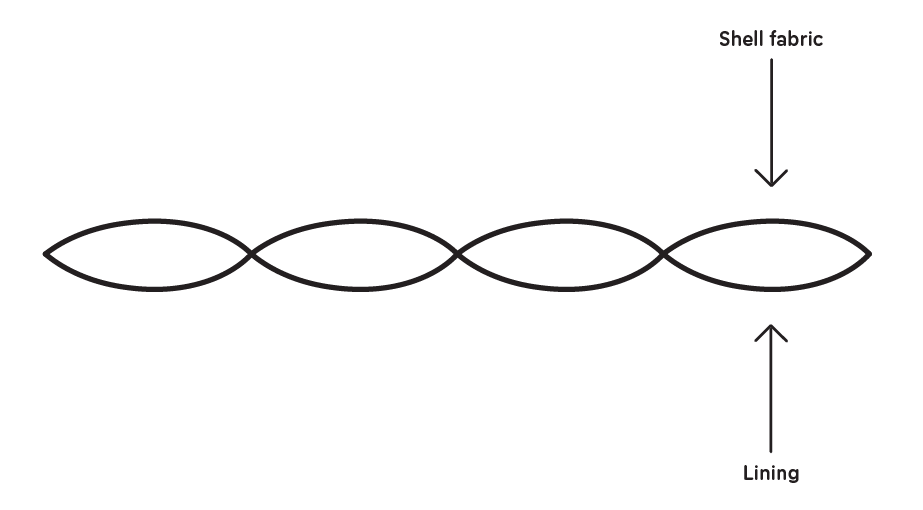
The second structure uses a box construction. There is a mesh fabric used as a spacer between the columns of down. This minimises cold spots, but due to the extra production complexity it’s more expensive.
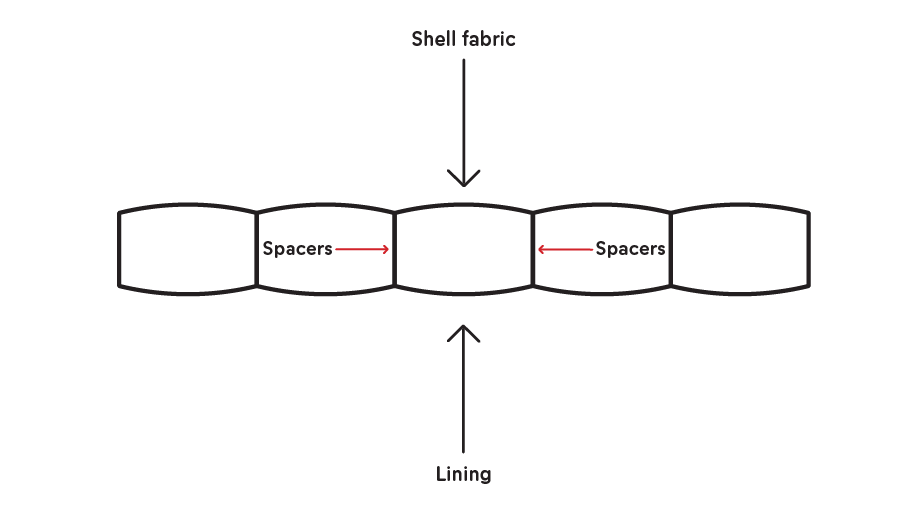
The final technique we use at Fjällräven is an offset construction. “We create two layers of sew-through-constructed down but we align column over stitch so there are no cold spots. This makes the jacket extremely warm, as air is trapped between the two layers as well as within the columns of down. But it’s more expensive because of the complicated production technique,” says Shufei.
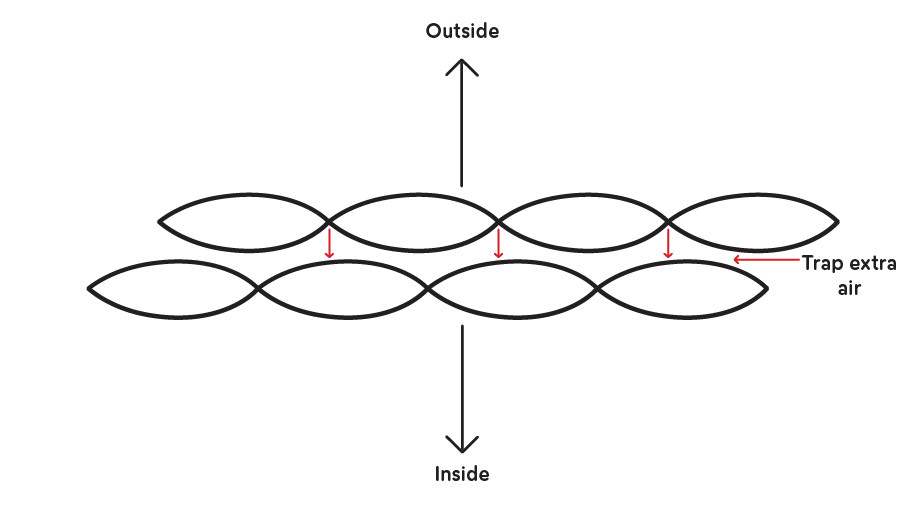
The material we choose for the outer fabric, whether a lightweight shell or the more heavyweight G-1000, also affects the insulating power of the jacket. And we sometimes use synthetic down to reinforce certain areas of a jacket that need to have water resistance or stand up to tougher wear, for example on the shoulders and elbows of our Keb Expedition Down Jacket.
Our Down Promise
As we’ve developed different structure techniques, new outer materials and expanded our use of down, we’ve learned a thing or two about the sourcing process. But in 2009 we started delving a lot deeper and we found that there was room for improvement. We began developing strict guidelines for how we source and handle our down. The result was our Down Promise with 100% traceability in our down chain. This means we can trace the down in our jackets right back to the farm where the birds lived.
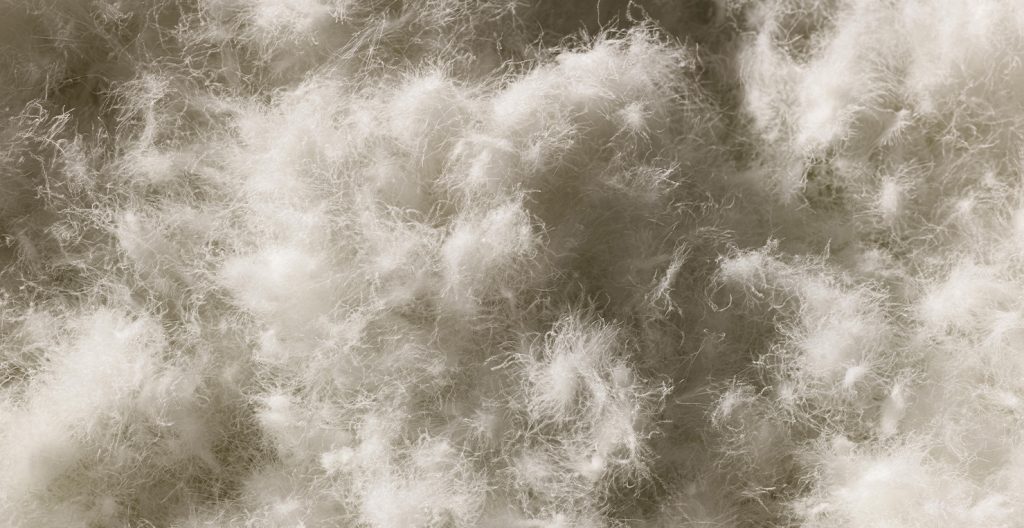
Our down is a by-product of the food industry. The feathers are taken from slaughtered geese with absolutely no live plucking. We also have a constant dialogue with our suppliers – and they must adhere to our Code of Conduct – to ensure high animal welfare standards. But because this isn’t enough, we’ve chosen to simplify the process to minimise risks. So we work with just one down supplier, who works with only a few selected farms and just one slaughterhouse. Our down is also stored separately in specially marked bags to avoid being mixed with other down. We have our own team of auditors that oversees the process and conducts both announced and unannounced checks.
We visit the farms; we know how the eggs are laid; how the fledglings hatch; how the goslings are raised, and we control how the birds are kept and what they are fed.
Aiko Bode
Chief Sustainability Officer, Fjällräven
And we now have one of the best down standards in the outdoor industry. But we don’t sit back and relax knowing we’re doing a good job. We’re constantly looking for improvements.
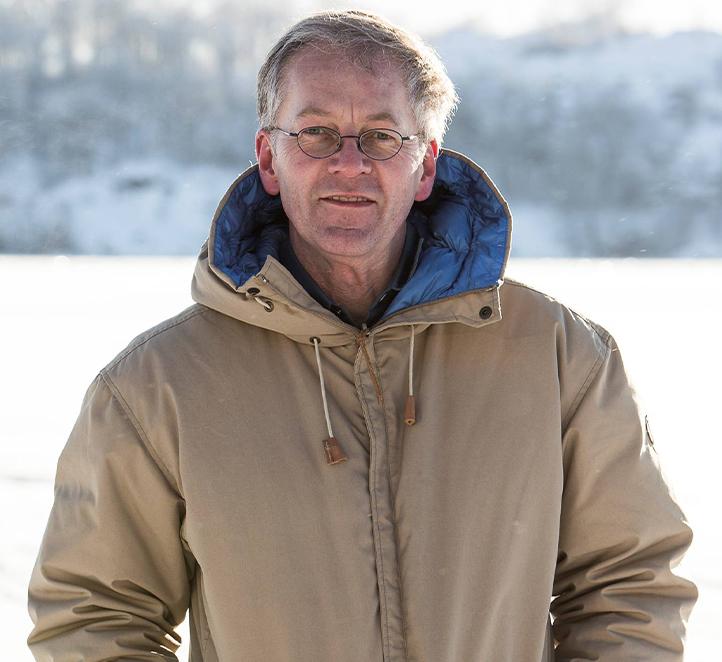
Aiko Bode Chief Sustainability Officer, Fjällräven
At Fjällräven, we always want to ‘leave the basecamp in better condition than we found it’. This drives us to always do better and, we hope, to push the outdoor industry into greater harmony with the very nature we love to explore. We’ve been working with provincial governments in China, where we source our down from, and our high-quality process with strict standards has now set local and regional animal welfare regulations. But we continue to listen, work with NGOs and the UN for ever-more transparent working conditions to ensure our down remains the best in the industry.
So not only will you be able to wrap yourself in the warming embrace of one of our down jackets on a cold winter’s night. You’ll be able to do so with a clear conscience, knowing that with our Down Promise your jacket is made from only ethically produced down of the highest quality.
More stories
Development